DC Motor Investigatory Project PDF (XII)

INTRODUCTION
A DC motor is any of a class of rotary electrical machines that converts direct current electrical energy into mechanical energy. The most common types rely on the forces produced by magnetic fields. Nearly all types of DC motors have some internal mechanism, either electromechanical or electronic, to periodically change the direction of current flow in part of the motor.
DC motors were the first type widely used, since they could be powered from existing direct-current lighting power distribution systems. A DC motor’s speed can be controlled over a wide range, using either a variable supply voltage or by changing the strength of current in its field windings. Small DC motors are used in tools, toys, and appliances. The universal motor can operate on direct current but is a lightweight brushed motor used for portable power tools and appliances. Larger DC motors are used in propulsion of electric vehicles, elevator and hoists, or in drives for steel rolling mills. The advent of power electronics has made replacement of DC motors with AC motors possible in many applications.
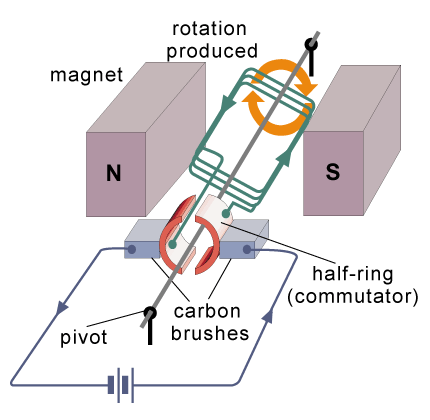
Evolution of DC Motor
The invention of the DC (direct current) motor can be attributed to multiple inventors and engineers who made significant contributions over:
- Michael Faraday (1821): Michael Faraday, an English scientist, discovered electromagnetic induction, which laid the foundation for the development of electric motors. Faraday demonstrated that a conductor moving through a magnetic field produced an electric current.
- William Sturgeon (1832): William Sturgeon, an English physicist, created the first practical DC electric motor. He constructed a device known as the “Sturgeon’s wheel,” which consisted of a rotating copper disc between the poles of a horseshoe magnet.
- Thomas Davenport (1834): Thomas Davenport, an American blacksmith and inventor, is credited with building the first practical DC motor in the United States. His motor used a rotary wheel design with a battery as the power source.
- Hippolyte Pixii (1832): Hippolyte Pixii, a French instrument maker, developed the first alternating current (AC) generator, known as the Pixii generator. While not a DC motor, it played a significant role in the advancement of electrical machines.
- Thomas Edison (1871): Thomas Edison, an American inventor, improved the design of the DC motor by developing a practical and efficient version. He received a patent for his DC motor design, which featured a multipolar armature and a commutator.
- Nikola Tesla (1888): Nikola Tesla, a Serbian-American inventor and engineer, introduced the concept of the induction motor, which operates on AC. Although not directly related to the DC motor, Tesla’s work on alternating current had a profound impact on the development of electrical machines.
- Frank J. Sprague (1886): Frank J. Sprague, an American engineer and inventor, made significant advancements in DC motor technology. He developed the first successful DC traction system for electric streetcars, using multiple parallel-connected motors for improved performance and control.
- Further Refinements: Over the years, engineers and inventors continued to refine and improve DC motor designs, focusing on aspects such as efficiency, control, and size. Advancements in materials, manufacturing techniques, and electronics led to the development of more compact, powerful, and efficient DC motors.
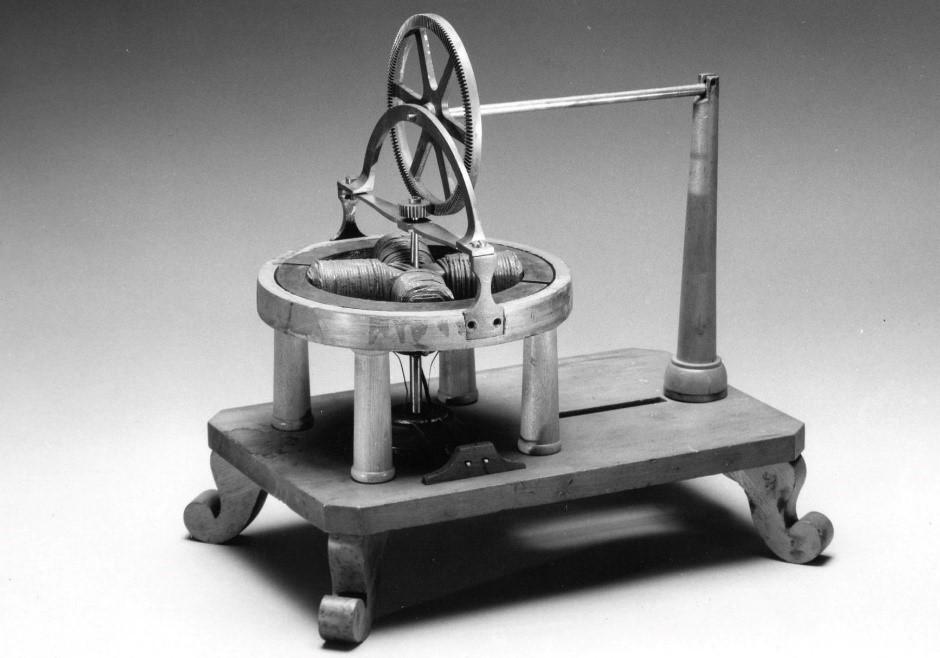
Working Principle of DC Motor
- Electric motor is a device which converts electrical energy into mechanical energy.
When a wire (coil) that carries current is placed in the region of
space that has magnetic field, the wire (coil) experiences a force.
The amount of force depends on:
1] The amount of current flowing in the wire/Loop
2] Length of wire/Number of loops
3] Strength of magnetic field
Direction of force depends on:
1] Direction of Current in the wire (Coil)
2] Direction of magnetic field
Note: – Fleming’s right-hand rule / Right hand palm rule is used to determine the direction of force if the direction of current and magnetic field is already known
How to build a Motor?
Materials Required:
- Cardboard
- 9V Battery
- Battery connector
- A round magnet (used in speakers)
- Some copper wire (0.2mm)
- 2 Thin Copper pin
- 2 Big safety pins
- On/Off switch
PROCEDURE
- Starting in the center of the wire, wrap the wire tightly and neatly around the marker 30 times.
- Slide off the coil you made on the marker.
- Wrap each loose end of the wire around the coil a few times to hold it together, then point the wires away from the loop, as shown below:
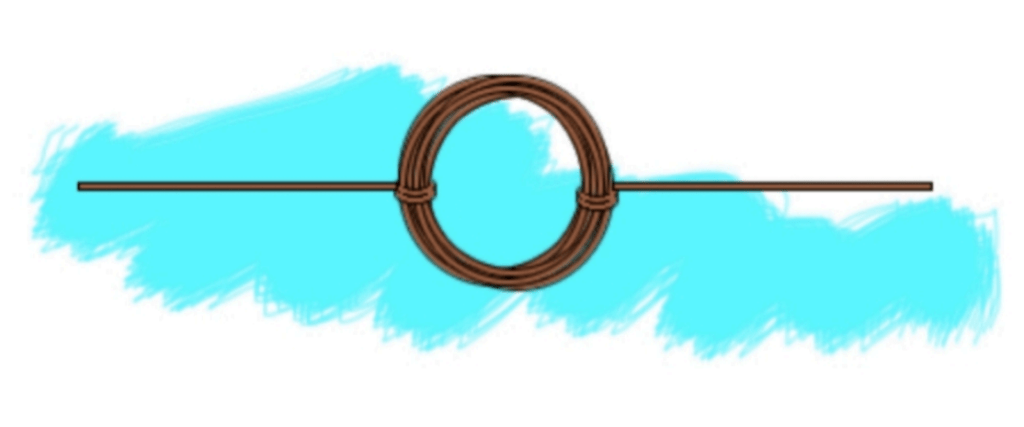
- Use knife to remove the wire insulation on each free end of the coil, as shown below:
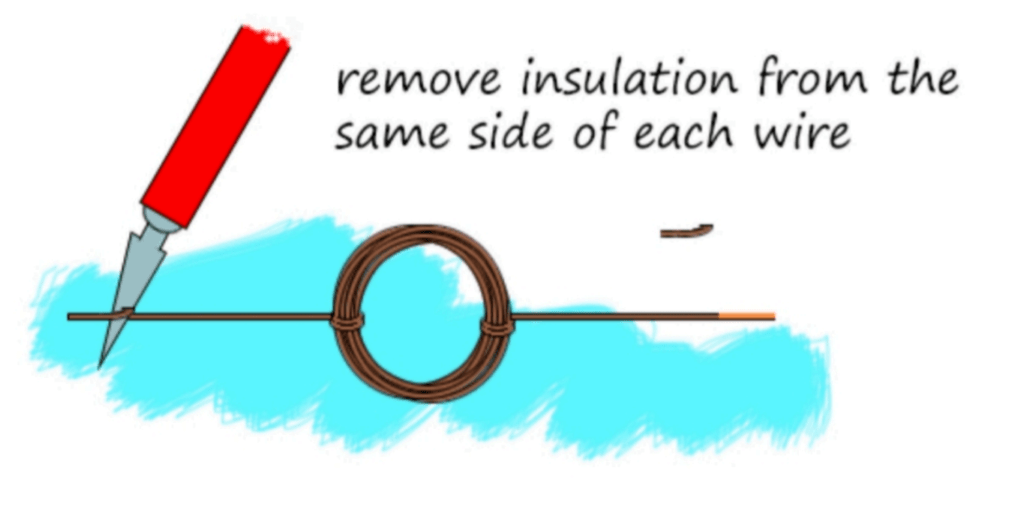
- Thread each loose end of the wire coil through the large eye of a needle. Try to keep the coil as straight as possible without bending the wire ends.
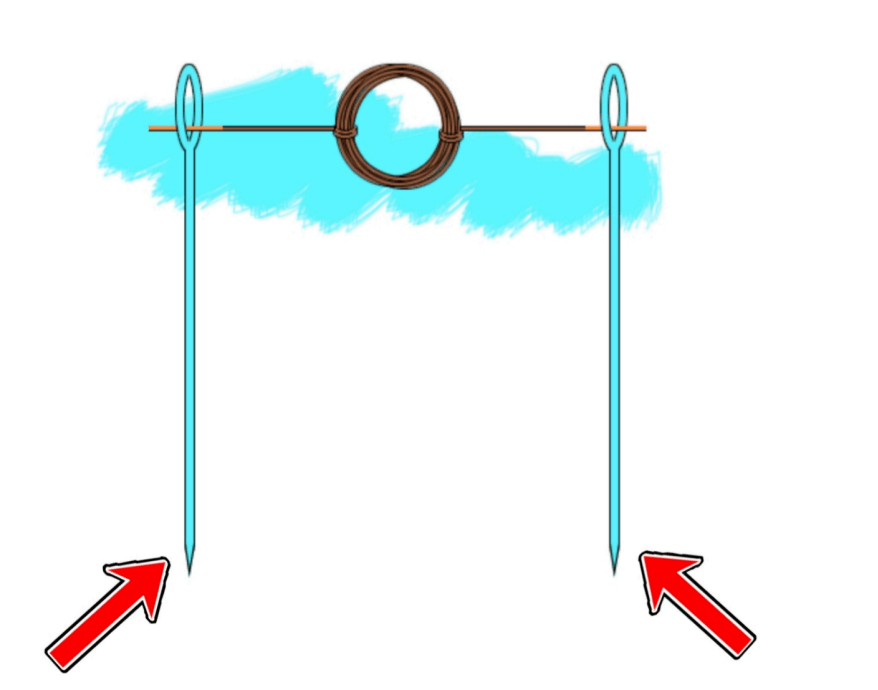
- Connect the battery across the two needles.
- Now place a magnet below the coil.
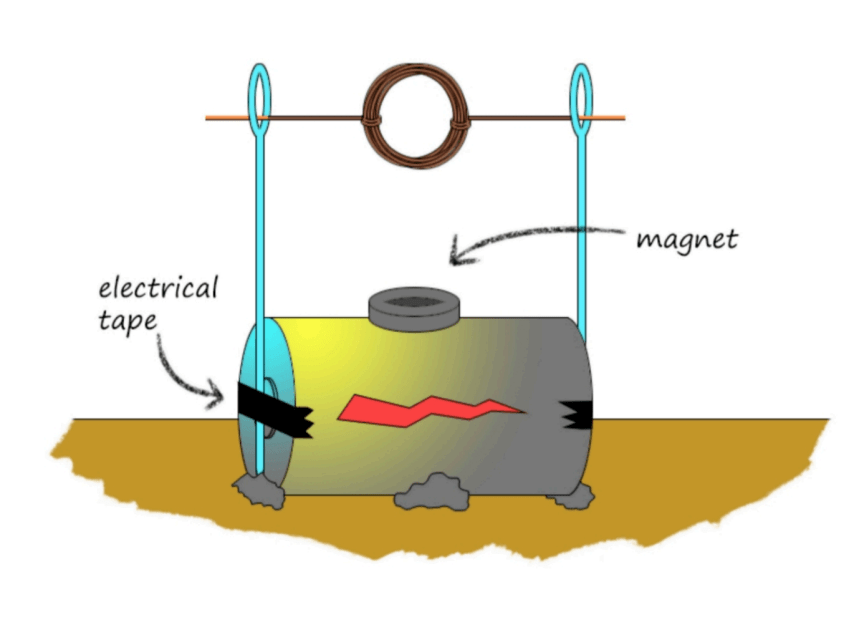
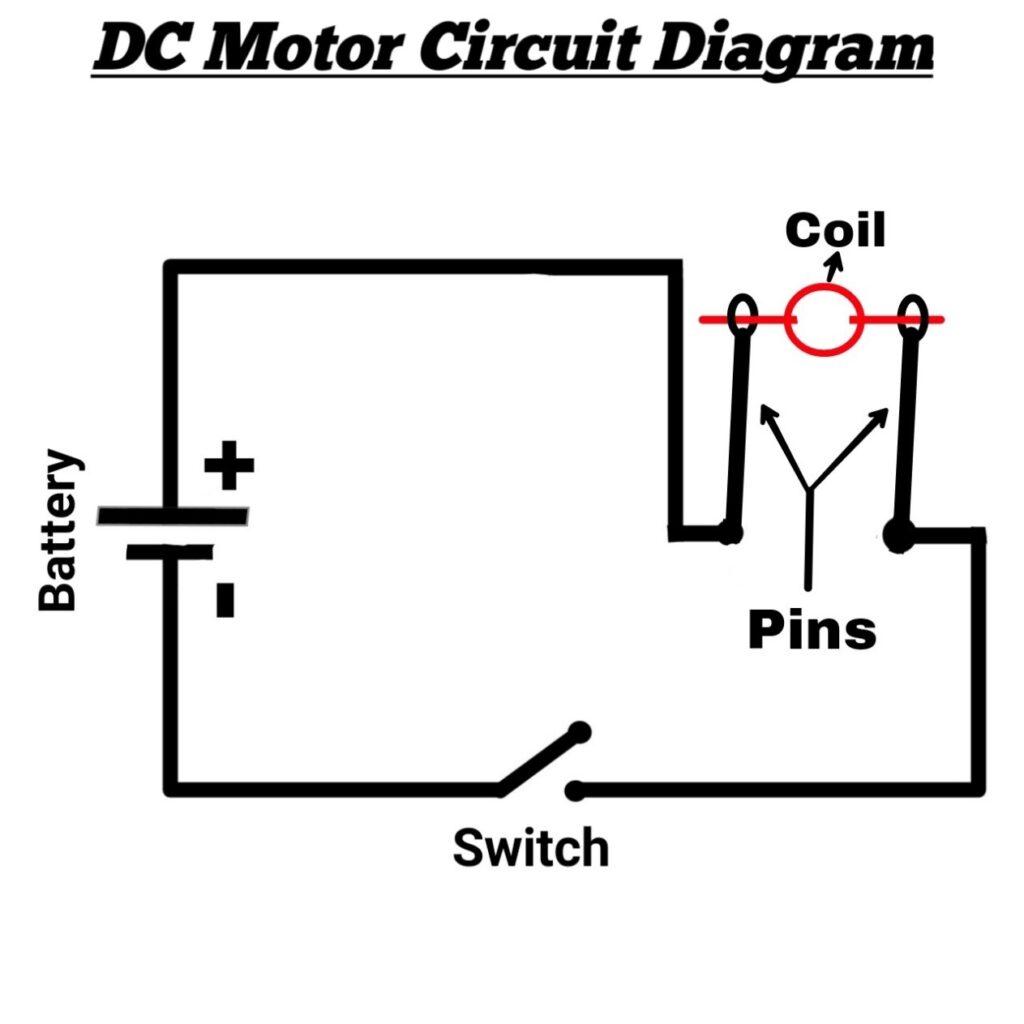
How DC Motor actually works?
The metal, needles, and wire created a closed loop circuit that can carry current. Current flows from the negative terminal of the battery, through the circuit, and to the positive terminal of the battery. Current in a closed loop also creates its own magnetic field, which you can determine by the “Right Hand Rule.” Making a “thumbs up” sign with your right hand, the thumb points in the direction of the current, and the curve of the fingers show which way the magnetic field is oriented.
In our case, current travels through the coil you created, which is called the armature of the motor. This current induces a magnetic field in the coil, which helps explain why the coil spins.
Magnets have two poles, north and south. North-south interactions stick together, and north-north and south-south interactions repel each other. Because the magnetic field created by the current in the wire is not perpendicular to the magnet taped to the battery, at least some part of the wire’s magnetic field will repel and cause the coil to continue to spin.
So why did we need to remove the insulation from only one side of each wire? We need a way to periodically break the circuit so that it pulses on and off in time with the rotation of the coil. Otherwise, the copper coil’s magnetic field would align with the magnet’s magnetic field and stop moving because both fields would attract each other. The way we set up our engine makes it so that whenever current is moving through the coil (giving it a magnetic field), the coil is in a good position to be repelled by the stationary magnet’s magnetic field. Whenever the coil isn’t being actively repelled (during those split-second intervals where the circuit is switched off), momentum carries it around until it’s in the right position to complete the circuit, induce a new magnetic field, and be repelled by the stationary magnet again.
Once moving, the coil can continue to spin until the battery is dead. The reason that the magnet only spins in one direction is because spinning in the wrong direction will not cause the magnetic fields to repel each other, but attract.
Troubleshooting
- Has the rotor been stripped correctly? Hold the plane of the loop so that it is oriented vertically. One of the straight sections of the rotor should be stripped completely (from rotor to end); the other straight section should be stripped on the top only.
- Is the circuit complete? Check each connection: red lead to thumbtack, thumbtack to paperclip, paperclip to stripped section of rotor, other stripped section of rotor to other paperclip, paperclip to thumbtack, thumbtack to black lead. Any break in the circuit will prevent current from flowing and thereby prevent motor from working.
- Is the rotor level and directly above the magnet? Adjust the rotor, paperclip supports and magnet until both straight sections of the rotor are perfectly horizontal, both paperclips supports are at the same height, and the magnet is directly underneath the rotor when the rotor is oriented so that the plane of the loop is vertical.
- Is the rotor close to the magnet? The magnetic field is strongest nearest to the magnet. When the plane of the rotor is oriented vertically, the bottom of the rotor should be as close to the magnet (without touching) as possible.
- Is the battery providing power? Use a voltmeter or multi-meter to check the voltage of the battery or simply replace with a fresh 9-volt battery.
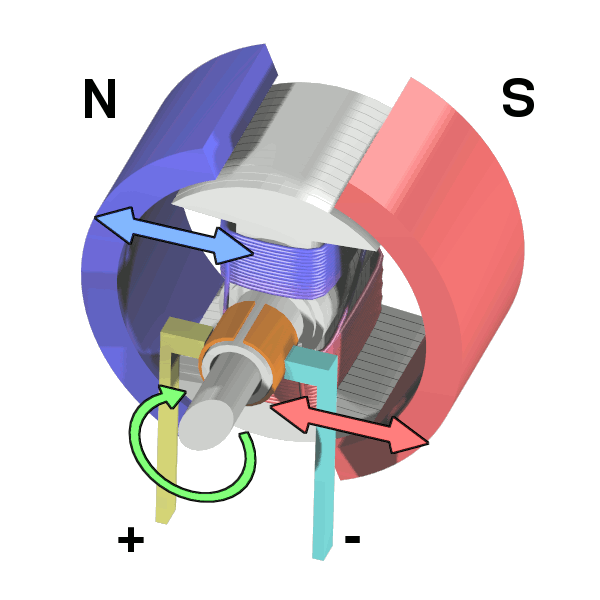
Application of DC Motor
- Electric vehicles: DC motors are used in electric cars and motorcycles to drive the wheels efficiently.
- Robotics: DC motors provide the necessary torque and speed control for robotic systems, enabling precise movements.
- Industrial machinery: DC motors are found in conveyors, pumps, mixers, and other industrial equipment, providing reliable power transmission.
- HVAC systems: DC motors are used in fans, blowers, and air conditioning units to regulate airflow and temperature control.
- Aerospace industry: DC motors are utilized in aircraft systems for applications such as fuel pumps, flap control, and landing gear operation.
- Medical devices: DC motors power various medical equipment, including surgical tools, centrifuges, and prosthetic limbs.
- Computer peripherals: DC motors are employed in printers, scanners, disk drives, and other computer hardware components.
- Home appliances: DC motors are used in appliances like washing machines, refrigerators, and vacuum cleaners for tasks such as agitating, compressing, and suction.
- Electric power tools: DC motors drive power tools such as drills, saws, and screwdrivers, providing high torque and control.
- Actuators: DC motors act as actuators in control systems, allowing precise movement and positioning in applications like valves, dampers, and servomechanisms.
- Textile industry: DC motors drive spinning machines, looms, and other textile machinery, facilitating the production process.
- Electric bicycles: DC motors power electric bicycles, assisting with pedalling and providing additional speed.
- Camera lenses: DC motors are used in autofocus mechanisms in cameras, enabling quick and accurate focusing.
- Electric gates and garage doors: DC motors drive the opening and closing mechanisms in gates and garage doors for convenient access control.
- Toys and entertainment: DC motors are utilized in various toys, including remote-controlled cars, model trains, and drones, providing motion and functionality.
Precautions
- All the connection should be neat and tight.
- Remove the insulation of the copper wire at both tips.
- Make sure the magnet used is enough strong to rotate the coil continuously.
- The copper wire should not be thicker than 0.2mm
- If the coil is not rotating by itself, just give a push to rotate.
- The coil should be oriented in the balance position.
- The coil should be balance in such a way that its all mass is on to the both pin
- Make sure you don’t use Iron pin in the coil
BIBLIOGRAPHY
- wikipedia.com
- Google search engine
- youtube.com
- Physics NCERT book for class XII
- http://tlaphysicsportfolio.weebly.com/
DC Motor Investigatory Project PDF (XII) Download Link